Air Cmde M S Rama Mohan, VSM & Brig (Dr) Anand Tewari (Retd)
Air Commodore M S Rama Mohan, VSM is pursuing PhD in Relevance of Multilateral Export Control Regimes and Policy Implications for India. He is a Flight Test Engineer and has participated in several flight test trials. He is presently posted to Air Headquarters.
Brig Anand Kumar Tewari (Retd) has 33 years of vast experience in Educational Administration. He completed his PhD from the University of Pune in Chinese Geopolitics and recently published a very contemporary Book – ‘Chinese Geopolitics in the 21st Century-A Post-Pandemic Perspective’. He has also been a Chinese language interpreter and is a recipient of the Chief of Army Staff Commendation Card. He now leads the AIDSS at Amity University, Noida as a Professor & Director.
Abstract
Additive manufacturing has changed the character of warfare. On-demand manufacturing of parts for end-use, shortening the supply chain, and improving the battlefield readiness of equipment are some use cases of additive manufacturing in recent conflicts. The use cases are restricted to non-critical areas. The barriers to extending additive manufacturing to the aerospace and defence sector require a regulatory framework for qualification and certification, testing and validation infrastructure and a trained workforce. India has promulgated a national strategy for applying additive manufacturing in the defence sector. Substantial use of additive manufacturing in joint warfare scenarios must be evolved by aligning with the national strategy. The paper assesses the barriers to the widespread use of additive manufacturing. It reviews India’s status of additive manufacturing before giving a few policy recommendations for accelerating the use of additive manufacturing in the armed forces.
Introduction
Technology is changing the character of warfare. New methods, weapons, and technology have evolved to wage war and gain an advantage over the adversary. Conventional to nonconventional weapons intersecting the conflict zone to no-war-no peace zone have been practised. Recent armed conflicts have demonstrated the ingenious application of technology to defeat conventional weapons. Technology has disrupted the traditional approaches to warfare in all domains – land, sea, and air. Additive manufacturing is one of the emerging technologies that has disrupted conventional warfare. Some quarters have assigned additive manufacturing as a strategic enabler in next-generation warfare. The emerging technology of additive manufacturing may be an enabler that could change the face of warfare. Still, it must cover a long maturation cycle and demonstrate its ability in different armed conflict scenarios. The paper analyses the operational challenges and barriers to implementing additive manufacturing in a full-blown armed conflict and examines the opportunities for military strategists and technologists. The paper covers the status of additive manufacturing in the Indian armed forces. It concludes with a few policy recommendations so that the potential of additive manufacturing can be harnessed in joint warfare scenarios.
Literature Review
Many quality technical papers, book chapters, and news media articles on additive manufacturing were reviewed. The literature ranged from fundamental research to diverse applications of additive manufacturing. Each paper covered the basics, advantages and disadvantages of additive manufacturing. Daniel M “Emerging Technology and Risk Analysis Additive Manufacturing” has brought out the science, technology, and use cases to ensure that additive manufacturing is acceptable and that technology will be affordable.1 This is an optimistic forecast for additive manufacturing technology, considering only the proliferation of technology. Micheal Kidd has argued that additive manufacturing, when deployed, will be a force multiplier in the “Additive Manufacturing Shaping the Sustainment Battlespace”.2 However, Henry A Colorado concluded in “Additive Manufacturing in Armour and Military Applications Research, Materials, Processing Technologies, Perspectives and Challenges” that additive manufacturing must overcome the challenges of the poor regulatory framework and lack of testing and validation infrastructure.3 The conclusion provides a user’s perspective, underscoring the widespread use of additive manufacturing. Frank Alifui-Segbaya in “Opportunities and Limitations of Additive Manufacturing that end-use applications of additive manufacturing can solve the scale-scope dilemma”.4 Having seen a diverse discourse on technology and use cases of additive manufacturing technology, Ajay Lele, in “Disruptive Technologies for the Militaries and Security”, stated that additive manufacturing reduces the logistical challenges and improves the tooth-tail ratio of militaries.5 Paneerselvam has made intuitive recommendations for additive manufacturing to benefit the Indigenous aerospace and defence sector.6 He further stated that the government must develop mechanisms to capture the changing nature of manufacturing in India. The literature does not cover the application of additive manufacturing in a military operational scenario. Considering the sensitivity of the knowledge, the scholarship may be silent. However, several news articles and corporate communication in the open domain claim that additive manufacturing has supported recent armed conflicts, which partially validates the application of additive manufacturing in armed conflicts. Therefore, there is a gap in understanding the operational barriers, which, if addressed, pave the way for additive manufacturing use in operational scenarios. The paper aims to identify the barriers to adopting additive manufacturing in warfare and recommends an approach for the focused and result-oriented application of additive manufacturing in joint warfare scenarios.
Additive Manufacturing
Additive Manufacturing (AM) is a process of joining materials to make parts from threedimensional model data, usually layer upon layer, as opposed to subtractive manufacturing and formative manufacturing methodologies.7 The Conventional Manufacturing (CM) process involves the removal of material or the forming of a shape using the material. Additive manufacturing, or three-dimensional printing (3DP) or Direct Digital Manufacturing (DDM), is an advanced manufacturing technique. Essential features of additive manufacturing in the context of aerospace and defence applications are
- Parts with complex geometries and shapes, such as aero-engine fuel system components, can be manufactured using additive manufacturing techniques. Polymers, metals, and ceramics are used as materials for the AM.
- Every part is printed using the three-dimensional geometric model as a computer code based on the computer-aided design drawing. Intended geometric and physical characteristics, namely dimensional tolerances, surface finish and the part’s material strength, are part of the computer code.
- The AM parts are lighter as no excess material is added to produce a form, while in conventional manufacturing, material is removed to produce a form. The excess material, if not removed in conventional manufacturing, adds to the weight of the part.8
- The manufacturing process involves the preparation, production, and post-production phases. No specific tools are required to be manufactured in the preparatory phase. Parts are produced in small batches per the computer program during the production phase. During the post-production phase, the surface finish is restored, or support material is removed.
- AM has moved the Technology Readiness Level from laboratory prototype to commercialised technology.9 Several challenges remain to be addressed.
- AM is a disruptive and path-breaking technology waiting to be adopted and exploited to its full potential, notwithstanding the challenges and barriers.10
Operational Advantages of AM
AM is considered to accelerate the development process from a prototype to a production standard. The tooling requirements are negligible. Selection of the material and the type of production is part of the design process, which in any case is aided by a computer. The production batch is small, and the lead time is less. Translate these features of the AM to operational scenarios, the following advantages will accrue: –
- The iterative cycle of the design-produce-validate-refine is short, implying that the response time between the prototype and the final product is short. Compression of time and cost encourages innovation in equipment in case of protracted armed conflicts when all the supply lines are disrupted, and one’s forces are under stress to achieve a breakthrough. Innovation of equipment using AM at the end-use location shortens the iterative cycle by directly considering the end-user’s experience. A product thus manufactured for the field on the field. A case in point is the addition of fins to grenades to stabilise its flight before hitting the target. The Ukrainian army improvised the grenade by attaching the fins printed by AM in the field location. The improvised grenades were installed on drones to mount attacks using the drones on the Russian armoured vehicles and tanks.
- Based on the computer program files, a part is manufactured for direct end-use in a remote location, away from the mass production sites. The end-use product using AM shortens the supply chain and reduces inventory costs. AM thus permits distributed manufacturing where the production facility is near the end-use location.11 The production facility may be on the front line, forward bases, or the logistics supply and support ships. Therefore, the response time for an on-demand production of a part is shorter than that of conventional manufacturing. Own forces could disrupt Colonel John Boyd’s Observe-Orient-Decide-Act (OODA) loop of the adversary by adopting the AM’s short rapid prototyping to rapid product delivery loop and the short decision loop.12 The advantage thus gained over the adversary by employing AM is significant.
- The strength of the AM lies in its computer programme and zero-tooling requirements, which can be customised to the part production requirements. The lower cost of production in AM overcomes the scale economies, and flexibility and customisation address the scope of economies. Thus, AM beats the scope-scale dilemma, which otherwise impacts conventional manufacturing.13
- The AM also permits varying the mechanical and physical characteristics of the part across its cross-section through topology optimisation techniques, which is difficult to achieve in conventional manufacturing.14 Such a feature saves wastage and reduces weight without compromising strength, which is essential for aerospace and defence parts.
Limitations of AM
Limited choices of materials for AM will have operational implications.15 The limited material choices may affect the operating envelope of the part as its mechanical and physical properties may be optimised. Adhering to stringent geometric tolerances is difficult in the AM as variations between the production batches are common. Rework to restore the tolerances is a challenge, unlike in conventional manufacturing. Repeatability and traceability of the quality levels of the AM parts are difficult owing to the variations in the microstructure of the AM material.
The global standards for manufacturing, qualification, and certification of parts manufactured through AM are evolving.16 Conventional qualification and certification methods do not apply to AM-produced parts in terms of material properties and manufacturing processes. In such a scenario, evolving the route to the certification plan for a part manufactured under AM is difficult. Global standardisation organisations, such as ISO and ASTM, have taken steps to develop standards.17 However, the AM is still in a nascent absorption stage, particularly in the aerospace and defence sectors. Mass production of various parts in different sectors using AM is yet to happen. The AM is being applied at the low end of the value chain. “Parts of consequence” or critical and complex components have yet to be manufactured using AM techniques. Few parts of the aeroengine fuel system have been attempted using the AM, with little success.
The proliferation of digital designs, materials, and ease of manufacturing are concerns of security apparatus in the military. The ease of hacking a digital design computer programme file and modifying it is a severe limitation to deploying AM in field conditions. The order of effect is unpredictable when the part manufactured by the hacked digital design is used by the adversary against its own forces.
Barriers to AM
With AM’s operational advantages and limitations, what are the barriers to AM becoming as widespread as conventional manufacturing? The barriers must be addressed when employing the AM in joint warfare scenarios.
- Global best practices and standards are essential for the aerospace and defence parts manufactured under AM. Separate material, mechanical, and environmental qualification and certification standards for AM parts are evolving. The prolonged lead times of certification and qualification, inadequate standards, rules and regulations and the high cost of certification are some of the decision points restricting the widespread use of AM parts in aerospace and defence.18 The testing and validation infrastructure for certification and qualification must be established based on the standards.19
- The AM parts are being used in non-critical aerospace and defence applications. The AM parts have yet to prove their worth in battle scenarios, though Ukraine has used them in its ongoing conflict with Russia at the low end of the value chain. Innovations in the form of medical devices like stethoscopes, prosthetics, personal protection equipment, body armour, fins for stabilising the flight of lofted grenades and drones were used by Ukraine in its conflict with Russia.
- Non-metal material for the AM parts has acquired certain acceptability, but AM technology for metal parts has yet to mature. The efficiency of the manufacturing, cost of manufacture, and availability of suitable materials for metal AM will result in increased absorption of metal AM parts.20
- The repeatability and reproducibility features of the AM must be improved. The accuracy of the manufacturing process must be improved, covering the material forming and printing stages. Since AM prints layer by layer, a variation in material property between two layers will result in poor process repeatability. Real-time monitoring, prediction, and control of the vital parameters of the manufacturing process, such as temperature, stress, microstructures, and mechanical properties of the printed parts, are essential for repeatability in AM.21 The feature of reproducibility must be harnessed for manufacturing legacy parts. Using the 3D scanning process and digitalisation of the legacy part, a new lease of life can be given to old and legacy systems by creating the spare parts. Sikorsky Utility helicopter UH-60L has been stripped open, and nearly 20,000 parts were scanned to identify replacement parts using AM.22
- AM uses a very high level of digitalisation from the design to the production stage. The computer-aided design files of the parts, printing machines, control and monitoring of the manufacturing process, digital inventory of the part files, and printing of the parts from a remote location are some steps involving digital technology in the AM. The level of digitalisation of AM is a barrier for smaller manufacturers to enter the AM domain, but it affords advantages over conventional manufacturing. Digitalisation also brings to the fore the intellectual property rights and license production aspects, which must be addressed legally.23
AM Use Cases
The AM was developed in 1984 to accelerate the prototype design and development process. In 1993, Soligen manufactured the first commercial 3D printer. By 2005, a highresolution printer was introduced. AM has been used for prototype development in aerospace and defence applications since 1988. The breakthrough for applying the AM to aerospace and defence equipment came with “Liberator”, a 0.308 calibre automatic firearm, printed from a CAD file in 2013.24 The firearm or gun did not print the firing pin and ammunition for apparent reasons. The time from design to full-scale development was progressively reduced from a few months to a few days. Rapid prototype development, therefore, was the central theme for the development of the AM. The initial stages of the AM polymers were used as feedstock for AM.25 Ceramics and metals were also introduced for the AM. The cost of AM’s “printing” equipment and the material to manufacture the parts have also been reduced significantly. Prompted by its affordability and advantages, AM was applied to aerospace and defence applications.
In the ongoing Ukraine-Russia conflict, additive manufacturing printers were installed to overcome the shortage of spare parts and critical components across the Ukrainian force’s diverse fleet of war equipment. Australia has donated three WarpSPEE3D metal 3D printers to Ukraine in Sep 2023.26 The 3D printers manufactured the “parts of consequences” or critical parts, a shortage of which may halt an operation or disrupt a mission. The hinge of the door of a troop carrier and specialist tool for the M113 gun were some of the critical parts produced using the cold spray AM technique. Printing the critical components near the end-use location in a contested environment will positively impact the tempo of operations. The argument must be substantiated with the tangible benefits from the battlefield spread over a period, and any conclusion at this stage will be premature. The Israel-Hamas conflict has also seen the use of application of the AM techniques in the conduct of the operations. In Oct 2023, patient-specific instruments were manufactured using 3DP by an Israeli company, Synergy3DMed, to treat wounded civilians and IDF soldiers.27 In Aug 2023, IDF seized a few pistols, rifles and weapon parts besides eight 3D printers. These developments in the Isael-Hamas conflict show the improvisation in battlefield tactics using emerging technologies such as AM. In the Nagorno-Karabakh conflict of 2020, a swarm of drones manufactured using the 3DP was used to attack the military command posts of the air defence systems, thereby immobilising the air defence systems.
Australia has used AM to repair the rudder anti-rotation bracket on the F/A-18 fighter aircraft and the landing gear shell bracket of a C-130 J transport aircraft.28 Concepts of lighter and stiffer designs with topology optimisation (alignment of the microstructure of the part’s metal) were employed in the AM of the parts. The parts have been qualified and certified for airworthiness, a milestone development. Notwithstanding, the airworthiness certification is a long-drawn process. In Nov 2022, the US Navy conducted trials to manufacture damaged or repaired parts by installing a 3D printer onboard USS Essex.29 Later, in Nov 2023, another printer was installed on the USS Bataan, an amphibious assault ship. The US Navy has ensured a supply of legacy parts on demand, shortening the supply chain. US Airforce uses 3D printing to manufacture obsolete parts for several legacy fighter jets, including fleets of B-52 bombers, the B-2 Stealth Bomber and C-5 Super Galaxy transport aircraft.30 In a significant development, the US Army has five large-scale machines capable of printing concrete. US Army has built two 512-square-foot buildings. Another project that the US Army has started is the jointless hull project for the underside of the vehicles. The Brazilian Air Force has used 3D printers for aerothermodynamics and experiments in hypersonic regimes. The 3D printers manufactured aircraft models and hypersonic engine prototypes for feasibility tests.
A critical use case of AM is parts replacement and reverse engineering. Various countries are progressively realising the potential of this feature of the AM. Digital twin technology, a digital representation of hardware, part, or component, is used in the AM technique for reverse engineering. The digital twin technology recommends processes to generate the hardware’s physical, metallurgical and mechanical data for reverse engineering. The digital twin application to AM involves the Internet of Things, AI / ML, and cloud computing concepts to ensure that the AM digitally re-constructs legacy hardware with acceptable accuracy and precision.31 As the idea amalgamates several cutting-edge technologies, the digital twinning application is in the research stage.32
Status of AM in India
India has responded to the changing manufacturing dynamic and its implications on national security. The strategic nature of the AM and its application in the Indian armed forces has been recognised by the Indian industry and strategic community. National Strategy for Additive Manufacturing issued by the Government of India in February 2022 is a policy-level response to the AM.33 The strategy aims to integrate seamlessly into the global AM architecture while ensuring India attains a global AM hub status. The strategy covers the defence and public sector for AM implementation and identifies aims to address critical challenges for AM in India. The strategy is aligned with the objectives of the Atma Nirbhar Bharat Abhiyan and Make-In-India initiatives of the Government to make India self-reliant. The challenges for AM technology absorption in India are recognised in the strategy, which has opened the avenue for opportunities.
The industrial, research, and development ecosystem of AM in India has taken significant measures. The DRDO has constituted a specialist panel on material and manufacturing, emphasising digital manufacturing and the development of advanced materials.34 It has assigned the AM development to three of its, namely DMRL, DRDL and R & DE. Fuel nozzles in a small turbofan engine used in the weapon systems were manufactured.35 In another case, a radio frequency transmitter-receiver antenna was manufactured by AM. The design, manufacture and post-processing process was completed in less than a week.36 DRDO uses AM to manufacture critical components for missiles, aircraft, handheld weapons, and drones. In another area, CEMILAC, the airworthiness agency under DRDO, has indigenised several polymers, composites and metal alloys that can be used for AM.37 A chapter has been introduced in the Indian Military Technical Airworthiness Regulations for the development of materials for the AM. A non-critical AM part has been certified and has already been deployed. CEMILAC is adopting a similar approach to certify a critical part. In Dec 2022, CEMILAC entered an MoU with ASTM to establish a qualification test framework for certifying AM parts, machine and material qualification processes, postprocessing, and part qualification.38 This is a significant development in the field of AM in India.
Agnikul Cosmos, an indigenous start-up in the space domain, has developed a semicryogenic, fully 3D-printed rocket engine.39 The three services have also seized the opportunity to exploit the AM. A two-storey AM Dwelling Unit for soldiers at Ahmedabad Cantt was commissioned.40 This 3D-printed house is a disaster-resilient structure that complies with Zone-3 earthquake specifications and green building norms. IAF signed an MoU with IIT Palakkad on 18 July 2022 for cooperation in aviation components with the specific aim of undertaking research in 3D Metal Additive Manufacturing.41 This cooperation between IAF and academia will enhance the AM usage in the Base Repair Depots of IAF for maintenance and repair functions. On Nov 22, the Indian Navy installed a 3D printer on its medium-sized frigate.42 The 3D printer is an industrial-grade metal printer.
Way ahead for India
The AM in India is in its nascent stage. Measures taken by the government encourage research and development in additive manufacturing. Fostering the growth of the additive manufacturing industry requires a whole-of-the-government approach as India aspires to contribute 25% of its GDP to the manufacturing sector. A focused approach for applying AM in the joint warfare scenario is required. The aim of the approach must be to move up the value chain of AM, progressively shortening the OODA loop of an adversary by rapid replenishment, rapid prototyping and rapid recovery of capability suffered due to battle damage in a time-bound and result-oriented manner. Considering the maturity of the AM and its implications, the approach may have short-term objectives with a perspective of three to five years and long-term objectives with a standpoint of eight to ten years. The following points are suggested for the approach.
- Along the lines of the National Strategy for Additive Manufacturing, the Joint Strategy for Additive Manufacturing must be evolved for all three services. The strategy may nominate a lead service and assign each service a core domain within additive manufacturing. Academic institutions, defence R & D organisations and the indigenous private sector must be part of the joint strategy. A consortium route for applying AM in joint warfare scenarios should be adopted.
- DIAT should be nominated as the nodal agency for applied research of AM in the operational scenarios. MoUs with leading academic institutions such as IIT Madras and research institutions such as Central Mechanical Engineering Research Institute and private industry may be executed. The research must cover materials, manufacturing processes, sensors for real-time monitoring and control, and quality assurance and certification. Three services should present problem statements for focused and result-oriented research outcomes from short- and long-term perspectives.
- Centres of excellence in additive manufacturing may be created in each service. Three services must actively include additive manufacturing in maintenance, repair and operational logistics activities. The repair organisations of all three services, including army base workshops, dockyards, aircraft yards, and base repair depots, must adopt additive manufacturing aggressively. A proof-of-concept project may be taken up in a short-term perspective.
- The services must develop a roadmap for progressively absorbing additive manufacturing in the operational scenarios. The roadmap must include a plan to utilise AM parts in battle damage repair instances, joint exercises, or joint warfare scenarios. Battle damages may be simulated to exercise the potential of the AM in terms of the time to recover, cost incurred, assurance of quality and functionality.
- Qualification and certification regulatory framework must be evolved to remove the barrier to deploying the AM parts in the conflict zone. Conventional QA and certification agencies should develop a lean, cost-effective, pragmatic framework from a long-term perspective. The framework must be producer- and user-friendly and conform to local conditions.
Conclusion
The potential of the AM will only be fully harnessed, and the AM will be accepted by services only when the AM parts survive the challenges of the battlefield. Towards this, the three services, academia, and industry, must strive to exploit the potential of the AM. A focused approach by these agencies will ensure that the application of the AM achieves the desired end state of gaining technological and strategic advantage over the adversary till the advent of a new emerging technology. Till then, AM will remain a technology demonstrator only.
DISCLAIMER
The paper is author’s individual scholastic articulation and does not necessarily reflect the views of CENJOWS. The author certifies that the article is original in content, unpublished and it has not been submitted for publication/ web upload elsewhere and that the facts and figures quoted are duly referenced, as needed and are believed to be correct.
*This paper was originally published in CENJOWS SYNERGY Journal [Vol 3 Issue 2] Aug 2024 Edition.
ENDNOTES
- Daniel M. Gerstein, Erin N. Leidy, “Emerging Technology and Risk Analysis”, Homeland Security Operational Analysis Center, RAND Corporation, Research Report, 2024, Available at https://www.rand.org/pubs/research_reports/RRA2380-1.html, Accessed on 07 Jun 2024.
- Micheal Kidd, Angela Quinn, and Andres Munera, “ Additive Manufacturing Shaping the Sustainment Battlespace”, Joint Force Quarterly, 4th Quarter, 2018, National Defence University Press, November 05, 2018, Available at https://ndupress.ndu.edu/Media/News/News–Article–View/Article/1681686/additivemanufacturing–shaping–the–sustainment–battlespace/, Accessed on 07 Jun , 2024.
- Colorado, Henry & Cardenas, Carlos & Gutierrez-Velazquez, Elkin & Escobedo, Juan & Monteiro, Sergio, “Additive Manufacturing in Armor and Military Applications: Research, Materials, Processing Technologies, Perspectives, and Challenges”, Journal of Material Research and Technology, 27(2023), Elsevier, https://doi.org/10.1016/j.jmrt.2023.11.030, Available at https://www.researchgate.net/publication/375926162_Additive_manufacturing_in_armor_and_military _applications_research_materials_processing_technologies_perspectives_and_challenges, Accessed on 07 Jun 2024.
- Frank Alifui-Segbaya, Inigo Flores Ituarte, Seymur Hasanov, Ankit Gupta, and Ismail Fidan,
“Opportunities and Limitations in Additive Manufacturing, “ in Pei, E., et al. Springer Handbook of Additive Manufacturing, Springer Handbooks, Springer, Cham. https://doi.org/10.1007/978–3–031–207525_9, Accessed on 07 Jun 2024.
- Lele, “Disruptive Technologies for the Militaries and Security”, Smart Innovation, Systems and Technologies, 132, Springer, https://doi.org/10.1007/978-981-13-3384-2_5, Accessed on 07 Jun 2024.
- Prakash Panneerselvam, “Additive Manufacturing in Aerospace and Defence Sector Strategy of India”, Journal of Defence Studies, Vol. 12, No. 1, January–March 2018, pp. 39–60, Available at https://www.idsa.in/system/files/jds/jds–12–1–2018–additive–pdf, Accessed on 07 Jun 2024.
- ISO/ASTM 52900:2021(EN), Additive manufacturing — General principles — Fundamentals and vocabulary, 2021, International Organisation for Standardisation, Geneva Available from: https://www.iso.org/obp/ui/#!iso:std:74514:en , Accessed on 03 Jun 2024.
- Pedro Espadinha-Cruz, Angela Neves, Florinda Matos, Radu Godina, “Development of a maturity model for additive manufacturing: A conceptual model proposal”, Heliyon, Vol 9, Issue 5.E16099, May 2023, DOI:https://doi.org/10.1016/j.heliyon.2023.e16099, Available at https://www.sciencedirect.com/science/article/pii/S2405844023033066, Accessed on 07 Jun 2024.
- European Patent Office, “ Innovation trends in additive manufacturing Patents in 3D printing technologies”, Sep 2023, pp 15 Available at https://www.epo.org/en/servicesupport/publications?size=n_10_n&filters%5B0%5D%5Bfield%5D=node_id&filters%5B0%5D%5Bvalues
- Brett Cooner, “Paradigm Shift Additive Manufacturing and the New Way of War”, Defence AT & L, November-December 2016, DAU, Vol 45, Number 6, pp 35-37, Available at https://apps.dtic.mil/sti/pdfs/AD1027005.pdf, Accessed on 07 Jun 2024.
- Ibid. Note 4, pp 131, and Petrick, I.J., Simpson, T.W.: 3D printing disrupts manufacturing: how economies of one create new rules of competition. Res. Technol. Manag. 56(6), 12–16 (2013)
- Jihong ZHU, Han ZHOU, Chuang WANG, Lu ZHOU, Shangqin YUAN, Weihong ZHANG, “A review of topology optimisation for additive manufacturing: Status and challenges”, Chinese Journal of Aeronautics, Volume 34, Issue 1, 2021, Pages 91-110, ISSN 1000-9361, https://doi.org/10.1016/j.cja.2020.09.020, Available at https://www.sciencedirect.com/science/article/pii/S1000936120304520, Accessed on 07 Jun 2024.
- In 2016, the AM facility saved an estimated €150,000 on jigs and fixtures – a figure that is expected to increase to €250,000 in 2017. Ben Redwood, Filemon Schöffer & Brian Garre, “The 3D Printing Handbook”, 3D Hubs V. Amsterdam, 2017, pp 287.
- Ze Chen, Changjun Han, Ming Gao, Sastry Yagnanna Kandukuri & Kun Zhou (2022) A review on qualification and certification for metal additive manufacturing, Virtual and Physical Prototyping, 17:2, 382-405, DOI: 10.1080/17452759.2021.2018938, Available at https://doi.org/10.1080/17452759.2021.2018938, Accessed on 07 Jun 2024.
- Rodney Brennen, “State of the PM Industry in North America—2023”, Metal Powder Industries Federation, New Jersy, 2023, pp 4, Available at https://www.mpif.org, Accessed on 07 Jun 2024
- Zhang, L., Zhou, W., Chen, X., “Digital Twins and Additive Manufacturing”, In: Lv, Z., Fersman, E. (eds) Digital Twins: Basics and Applications, Springer, Cham,2022, pp 27-35, https://doi.org/10.1007/978-3-03111401-4_4, Accessed on 07 Jun 2024.
- Sydney J. Freedberg Jr, “Army Dissects Black Hawk Helo, Scans Parts For 3D Printing”, Breaking Defense, Oct 15, 2020, Available at://breakingdefense.com/ 2020/10/army- Amr dissects-black-hawk-helo-scans-parts-for-3d-printing/, Accessed on 07 Jun 2024.
- “3D opportunity in the Department of Defense: Additive manufacturing fires up”, A Deloitte series on additive manufacturing, Deloitte University Press, 2014, Available at https://www2.deloitte.com/content/dam/insights/us/articles/additive-manufacturing-defense-3d- printing/DUP_1064-3D-Opportunity-DoD_MASTER1.pdf, Accessed on 07 Jun 2024.
Carolyn Schwaar, “Metal 3D Printers At Ukraine’s Frontlines Make Critical Spare Parts”, Forbes, 23 Sep 2023, Available at https://www.forbes.com/sites/carolynschwaar/2023/09/20/metal–3d–printers–atukraines–frontlines–make–critical–spare–parts/, Accessed on 07 Jun 2023.
“Revolutionary Israeli 3D Printing Technology Produces Custom Parts for Patients, Applied to Wounded IDF Soldiers”, Aurora, 16 May 2024, Available at https://aurora–israel.co.il/en/A–revolutionary–Israeli3D–printing–technology–produces–personalized–parts–for–patients–and–is–applied–to–wounded–IDFsoldiers/, Accessed on 07 Jun 2024.
Fact Sheet Department of Defence, Science and Technology, Australian Government, “ Additive Manufacturing”, DSC 2064, Aug 2018, Available at https://www.dst.defence.gov.au/publication/additive–manufacturing, Accessed on 07 Jun 2024.
- Jaren K. Price, Miranda C. La Bash, and Bart Land, “ 3D Printing for Joint Agile Operations”, Joint Force Quarterly, 4th Quarter, 2019, National Defence University Press, October 05, 2019, Available at https://ndupress.ndu.edu/Portals/68/Documents/jfq/jfq–95/jfq–95_92–99_Price–LaBash–Land.pdf/, Accessed on 07 Jun 2024
- “How are Different Branches of the US Military using Additive?”, Markforged, Available at https://markforged.com/resources/blog/how-are-different-branches-of-the-us-military-using- additive, Accessed on 07 Jun 2024.
- Shen, T., Li, B., “Digital twins in additive manufacturing: a state-of-the-art review”, Int J Adv Manuf Technol 131, 63–92 (2024). https://doi.org/10.1007/s00170-024-13092-y, Accessed on 07 Jun 2024.
- “National Strategy for Additive Manufacturing”, GoI, Ministry of Electronics and IT, Available at https://www.meity.gov.in/content/national-strategy-additive-manufacturing, Accessed on 07 Jun 2024.
- Materials & Manufacturing Panel, DRDO Available at https://www.drdo.gov.in/drdo/aeronautics- research-development/materials-manufacturing-panel, Accessed on 07 Jun 2024.
- Case Studies- Wipro 3D, “STFE Starting Nozzle”, Wipro 3D, Available at https://wipro-3d.com/industryapplication/metal-3d-printing-in-defense, Accessed on 07 Jun 2024.
- Ada Shaiknag, “AMSI Bangalore 2023: Airworthiness and certification of AM parts for defense and aerospace applications”, 3D Printing Industry, 23 Sep 2023, Available at https://3dprintingindustry.com/news/am-2023-airworthiness-and-certification-of-am-parts-for-defenseand-aerospace-applications-224799/
- Agnilet, AM developed a cryogenic rocket engine of 3kN. Several parts of have been captured in one single piece of the 3D printed hardware. Source https://agnikul.in/#/tech
- Aditya Chandavarkar,“The Growing Indian Additive Manufacturing Ecosystem: A Promising Frontier”, AM Chronicle, 21 November 2023, Available at https://amchronicle.com/insights/the–growing–indianadditive–manufacturing–ecosystem–a–promising–frontier/, Accessed on 07 Jun 2024
- “IIT-PKD signs MoU with IAF for 3D Metal Additive Manufacturing”, IIT-PKD, 25 Jul 2022, Available at https://iitpkd.ac.in/news/iit-pkd-signs-mou-iaf-3d-metal-additive-manufacturing, Accessed on 07 Jun 2024.
- Jaiharshvardhan Rathore, “Rapid Manufacturing in Naval Defense Engineering”,Medium, 04 Nov 2023, Available at https://medium.com/@jaiharshvardhan.rathore20/rapid-manufacturing- in-naval-defenseengineering-c5e06441102a, Accessed on 07 Jun 2024.
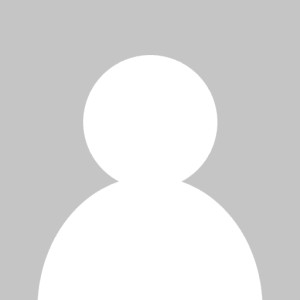
Air Commodore M S Rama Mohan, VSM
Air Commodore M S Rama Mohan, VSM is pursuing PhD in Relevance of Multilateral Export Control Regimes and Policy Implications for India. He is a Flight Test Engineer and has participated in several flight test trials. He is presently posted to Air Headquarters.
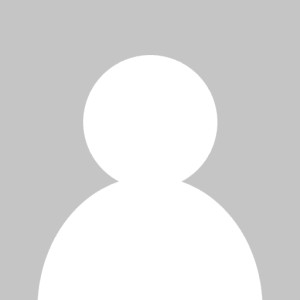
Brig Anand Kumar Tewari (Retd)
Brig Anand Kumar Tewari (Retd) has 33 years of vast experience in Educational Administration. He completed his PhD from the University of Pune in Chinese Geopolitics and recently published a very contemporary Book – ‘Chinese Geopolitics in the 21st Century-A Post-Pandemic Perspective’. He has also been a Chinese language interpreter and is a recipient of the Chief of Army Staff Commendation Card. He now leads the AIDSS at Amity University, Noida as a Professor & Director.